02
2024
-
01
Evaluation and selection of pretreatment process before ultrafiltration
Author:
Ultrafiltration cannot intercept and remove dissolved substances in water. Therefore, if it is necessary to use ultrafiltration technology to intercept and remove dissolved pollutants, they must be transformed into suspended or colloidal forms in the pre-treatment process of ultrafiltration.
If the pollutants in water are mainly microorganisms and particulate matter, usually only a small amount of pre-treatment measures are needed before ultrafiltration. Generally, pre filters (100-300) are installed upstream of the ultrafiltration process μ m) Removing larger particulate matter is sufficient, such as using self-cleaning filters, bag filters, filter cartridges, or disc filters.
Depending on the type of raw water or fluctuations in the quality of the ultrafiltration influent, other pre-treatment techniques can also be used before ultrafiltration, such as coagulation/flocculation, clarification/sedimentation, air flotation, or particle media filtration.
(1) Coagulation/flocculation
During the coagulation process, chemicals such as aluminum or iron salts are added to water, and the added agent is quickly stirred to diffuse in the water, reducing the repulsive force (destabilization) between particles and allowing them to adsorb and polymerize with each other. Correspondingly, the flocculation process belongs to low-intensity stirring to increase the rate of particle aggregation.
Coagulation and flocculation can use cationic, anionic, or non-ionic agents.
(2) Clarification/precipitation
Setting up clarification/sedimentation processes to reduce the concentration of particles or colloidal substances after coagulation/flocculation processes, or to remove settleable solids from turbid water, without adding coagulants.
This pre-treatment is generally used for influent with average turbidity>30NTU or peak turbidity>50NTU, and can obtain clear water with turbidity<2NTU and SDI<6
The hydraulic retention time of clarification/sedimentation tanks is generally 2-4 hours. The types of preprocessing include:
Efficient sedimentation tank (inclined plate sedimentation tank)
Adding inclined plates in conventional sedimentation tanks to provide a larger sedimentation area can more efficiently precipitate and remove suspended solids from water.
Generally used
60 ° inclination angle, using 5cm plate to plate spacing
The inclined plate setting of the distance has a higher sedimentation rate and a smaller footprint (usually 65-80% smaller than the footprint of a conventional sedimentation tank). The inclined plate sedimentation tank is suitable for treating influent with turbidity greater than 50NTU.
Carrier flocculation high-density sedimentation tank
Adding high-density insoluble media particles such as fine sand during the coagulation stage, utilizing the gravity settling effect of the medium and the adsorption effect of the carrier to accelerate the "growth" and sedimentation of flocs, belongs to a rapid precipitation technology.
Generally, high-density sedimentation tanks have advantages such as short sedimentation time, small footprint, and the ability to withstand high impact loads.
Dissolved Air Floatation Method (DAF)
By producing water microbubbles (<50) in the water μ m) And during the slow rise of microbubbles, they adsorb onto the condensed suspended solids, causing the density of the suspended solids to decrease and float to the water surface. Solid substances are removed on the surface of the purifier instead of the bottom (i.e. clarified water is discharged from the bottom instead of the top).
The area occupied by dissolved air flotation is generally smaller than that of conventional sedimentation tanks, and it can be used to remove light particles (such as condensed NOM), algae, or oils with influent turbidity less than 50NTU and slow sedimentation. Generally, clear water with turbidity less than 0.5NTU can be obtained.
(3) Media filtration
To remove particles, suspended solids, and colloids from water, water flows through one or more layers of granular media (such as sand, pumice, and anthracite). This is based on the fact that when water flows through the bed of the filter medium, particles, suspended solids, and colloids adhere to the surface of the filter medium.
The water quality of the effluent from granular media filtration depends on impurities, the size and shape of the filtering medium, surface charge and shape, raw water composition, and operating conditions. If designed and operated reasonably, media filtration can generally remove 90-99% of particles, suspended solids, and colloids.
There are several different types of granular media filtration:
Single medium filtration
Generally, fine sand is used, suitable for influent with turbidity<2NTU and TSS<3mg/L;
Multi media filtration
The most commonly used filtering media are quartz sand and anthracite. Fine sand filters have quartz sand particles with an effective diameter of 0.35-0.5mm, while anthracite filters
The effective diameter of the particles is 0.7-0.8mm.
When using a dual medium filter filled with anthracite on quartz sand, it allows suspended solids and other impurities to enter the interior of the filter layer, producing more effective deep filtration and extending the cleaning interval.
The minimum designed total bed depth of the filter medium is 0.8m. In a dual medium filter, quartz sand with a height of 0.5m and anthracite with a height of 0.4m are usually filled.
Dual stage media filtration
(Applicable to influent turbidity>20NTU and TOC>6mg/L)
Usually, the first stage is a coarse single medium or multi medium filter (which can remove 60-80% of suspended solids), while the second stage uses a polished dual medium filter, which can remove 99% of the remaining fine suspended solids.
The removal rate of TOC by two-stage media filtration is relatively low, usually only 20-30%. However, if an activated carbon layer is installed at the top, the removal efficiency of TOC can reach up to about 50%. Double stage media filtration can generally obtain produced water with a turbidity of less than 0.1 NTU.
In addition, media filtration systems can be classified according to different classification methods as follows:
By driving force:
Gravity filtration: a device that filters by the static pressure generated by the weight of the water flow itself.
Generally, a gravity filter is formed by placing a porous plate at an appropriate height at the bottom of the filter and laying the filter medium. Due to its low static pressure, it is only suitable for materials that are easy to filter or for operational processes that do not require high filtration rates.
Commonly used types include bag filters, sand filters, etc. Its operation is mostly intermittent.
Pressure filtration: Generally, closed steel filtration containers are used, which can withstand pressure and can use higher filtration bed layers, finer filtration medium particle sizes, and higher filtration rates. The designed filtration flow rate is usually less than 10-20m/h, and the backwash flow rate is 40-50m/h.
By filtering speed:
Slow filtration: Gravity filtration is the main method, and the filtration speed is generally less than 0.5m/h. It is usually suitable for influent with turbidity<5-10NTU and TOC<3mg/L, and can obtain filtered water with turbidity<1NTU.
Rapid filtration: It can be gravity filtration or pressurized filtration. The maximum filtration rate can reach 12m/h, and pre coagulation is usually required to obtain filtered water with a turbidity of less than 1 NTU.
High speed filtration: pressurized filtration, with a maximum filtration speed of up to 30m/h. Under the action of coagulants and coagulants, filtered water with a turbidity of less than 0.5 NTU can be obtained.
According to the direction of flow:
Downstream filtration: This type is most commonly used, where water flows through a filter layer from top to bottom for filtration.
Upstream filtration: Less commonly used, water flows from bottom to top through the filter layer for filtration.
Related Products
Biological nitrogen removal process of low temperature wastewater
2024-05-28
Prevention and treatment of calcium carbonate scaling in reverse osmosis operation
2024-05-22
Treatment of pyrazolone production wastewater - bipolar membrane electrodialysis process
2024-05-20
How much salt does sewage contain that can enter the biochemical system?
2024-05-17
Huanke Environmental Protection Technology
HOTLINE:
Address:Gongye 1st Street, Weicheng District, Weifang City, Shandong Province China
Contact:Zhang Gong
Phone:+86-18865361829
Email:sdhuanke@163.com
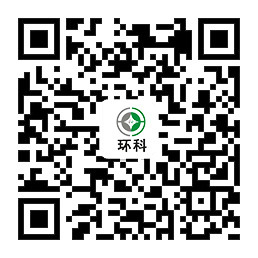
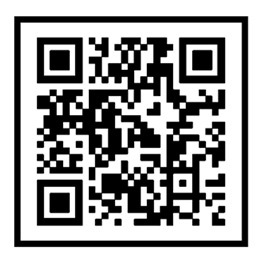
Consult
Copyright © 2023 Shandong Huanke Environmental Protection Technology Co., Ltd